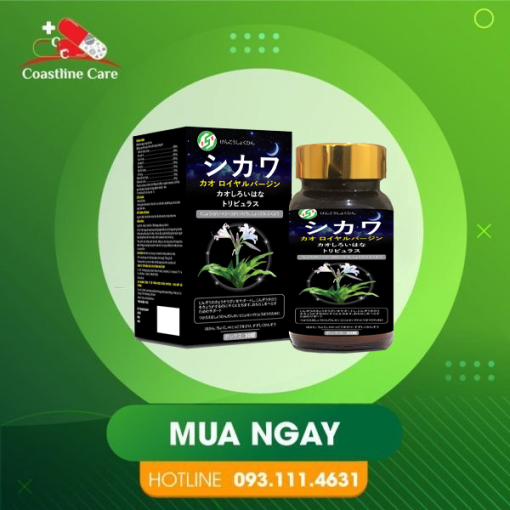
Discover the necessity of EMS audits in EHS management. Check out audit types, very best methods, and field worries to boost compliance and sustainability attempts.
Method – This branch contains each of the actions and treatments associated with the procedure or action, in addition to the gear, materials, and workflow.
During the manufacturing business, notably during the automotive and electronics sectors, the diagram is frequently used in steady improvement initiatives like Six Sigma and Lean Production.
The basic idea was to start with Utilized in the twenties, and is taken into account one of the 7 fundamental resources of good quality Regulate.[5] It is called a fishbone diagram on account of its form, comparable to the side look at of the fish skeleton.
It’s particularly beneficial for fast brainstorming classes or when introducing the thought of induce and influence Evaluation to All those unfamiliar with the fishbone methodology.
This kind of tracking listing will also be employed to communicate the group’s development to management and customers. New insights may very well be attained because the investigation progresses. One example is, any individual examining the duration of a part could possibly have noticed harm. This harm could then be entered into an up to date Ishikawa diagram and then transferred towards the monitoring record.
Visit the Gemba: Stop by the actual place where the situation takes place to observe firsthand, acquire exact information, and improved have an understanding of the underlying causes.
Attract the central spine: Lengthen a horizontal line from the condition for the remaining, nha thuoc tay symbolizing the diagram’s central “spine.”
Every of such branches is utilized to recognize probable results in that may be contributing to the trouble underneath investigation. Such as, if a decrease in solution high quality is the issue, the Ishikawa nha thuoc tay Diagram can be used to identify the various elements that might be triggering this issue, such as a deficiency of personnel schooling, faulty machines, or minimal-high-quality supplies.
Ishikawa diagrams were being popularized from the 1960s by Kaoru Ishikawa,[4] who pioneered top quality management procedures from the Kawasaki shipyards, and in the process turned one of several founding fathers of modern administration.
By facilitating systematic identification and categorization of causes, the Ishikawa fishbone diagram becomes An important Device in dilemma-solving and selection-producing processes.
Down below is surely an example of a fishbone diagram for any producing organization. Within this circumstance, the company employs the 6Ms to raised recognize the causes of the challenge, which is that a Portion of the product or service is in the wrong dimensions.
Ishikawa was also a solid advocate for high quality circles. A high quality circle is a group of staff who voluntarily fulfill consistently to debate and clear up complications related to their function. The idea was introduced in Japan inside the 1960s and have become a cornerstone of the standard movement.
Last but not least, working nha thuoc tay with Ishikawa Diagrams to unravel business enterprise complications can result in better procedures, bigger purchaser gratification, and a far more successful organisation. Teams can accomplish bigger achievements and propel their corporations ahead by mastering this strong Instrument.